8 innovative uses of augmented reality in manufacturing
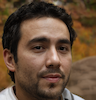

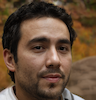
Augmented Reality in Manufacturing: Revolutionizing the Industry with 8 Innovative Uses
The manufacturing industry has undergone significan't transformations over the years, with the adoption of new technologies playing a crucial role in shaping its future. One such technology that is gaining traction is Augmented Reality (AR). AR has the potential to revolutionize the manufacturing industry by improving efficiency, reducing costs, and enhancing worker safety. In this article, we will explore eight innovative uses of AR in manufacturing that are transforming the industry.
Improving Assembly and Inspection Processes
One of the most significant challenges in manufacturing is ensuring that products are assembled correctly and efficiently. AR can help address this issue by providing workers with step-by-step assembly instructions and real-time quality control checks. For instance, aerospace manufacturer, Boeing, uses AR to guide workers during the assembly of complex aircraft parts. By using AR-enabled glasses, workers can view detailed instructions and videos that help them complete tasks more efficiently and accurately.
AR can also be used to inspect products during the manufacturing process. By using AR-enabled devices, quality control inspectors can view detailed 3D models of products and identify potential defects or issues. This enables them to take corrective action early on, reducing the likelihood of defects and improving overall product quality.
Enhancing Remote Collaboration and Training
AR can also facilitate remote collaboration and training in manufacturing. With the use of AR-enabled devices, experts can remotely guide workers through complex tasks, reducing the need for on-site visits and improving knowledge transfer. This is particularly beneficial for manufacturers with multiple production facilities or those that operate in remote locations.
For example, the German engineering company, Siemens, uses AR to provide remote training to its workers. By using AR-enabled devices, trainers can demonstrate complex tasks and provide workers with real-time feedback, improving their skills and knowledge.
Streamlining Warehouse Operations
AR can also be used to improve warehouse operations by providing workers with real-time inventory information and navigation assistance. This enables them to quickly locate and retrieve items, reducing search times and improving overall efficiency.
For instance, the logistics company, DHL, uses AR to guide warehouse workers during the picking and packing process. By using AR-enabled glasses, workers can view real-time inventory information and receive navigation assistance, improving their productivity and reducing errors.
Reducing Maintenance Downtime
AR can also be used to reduce maintenance downtime by providing workers with real-time access to maintenance manuals and repair guides. This enables them to quickly diagnose and repair equipment, reducing downtime and improving overall productivity.
For example, the industrial equipment manufacturer, GE Appliances, uses AR to provide workers with real-time access to maintenance manuals and repair guides. By using AR-enabled devices, workers can view detailed instructions and videos, reducing the time it takes to repair equipment and get production back online.
Improving Supply Chain Management
AR can also be used to improve supply chain management by providing manufacturers with real-time visibility into inventory levels and shipment status. This enables them to optimize their supply chain operations, reducing costs and improving overall efficiency.
For instance, the logistics company, Maersk, uses AR to provide real-time visibility into container inventory levels and shipment status. By using AR-enabled devices, manufacturers can track their shipments in real-time, improving their supply chain planning and optimization.
Enhancing Safety Training
AR can also be used to enhance safety training in manufacturing. By using AR-enabled devices, workers can participate in simulated training exercises that mimic real-world scenarios, improving their ability to respond to emergencies and reducing the risk of accidents.
For example, the oil and gas company, Chevron, uses AR to provide workers with safety training exercises that simulate real-world scenarios. By using AR-enabled devices, workers can practice responding to emergencies, such as fires and chemical spills, improving their safety skills and knowledge.
Improving Field Service Operations
AR can also be used to improve field service operations by providing technicians with real-time access to equipment information and repair guides. This enables them to quickly diagnose and repair equipment, reducing repair times and improving overall customer satisfaction.
For instance, the industrial equipment manufacturer, Caterpillar, uses AR to provide technicians with real-time access to equipment information and repair guides. By using AR-enabled devices, technicians can view detailed instructions and videos, reducing the time it takes to repair equipment and improving overall customer satisfaction.
Conclusion
The manufacturing industry is undergoing a significant transformation, driven by the adoption of new technologies such as Augmented Reality. AR has the potential to revolutionize the industry by improving efficiency, reducing costs, and enhancing worker safety. From improving assembly and inspection processes to enhancing remote collaboration and training, AR is being used in innovative ways to address some of the industry's most pressing challenges. As the technology continues to evolve, we can expect to see even more innovative uses of AR in manufacturing, driving growth and productivity in the industry.
Augmented reality is transforming the manufacturing sector in ways that were previously unimaginable. By overlaying digital information onto the physical world, manufacturers can streamline processes, improve efficiency, and reduce errors. From remote guidance to predictive maintenance, AR is revolutionizing the way products are designed, produced, and maintained. In this article, we'll explore eight innovative uses of AR in manufacturing that are changing the game.
1. Remote Guidance and Training
One of the most significant benefits of AR in manufacturing is its ability to provide remote guidance and training. By using AR-enabled devices, such as smart glasses or tablets, manufacturers can connect with experts from around the world in real-time. This allows for remote guidance on complex repairs, maintenance, and assembly, reducing the need for on-site visits and minimizing downtime.
For example, Boeing, the aerospace giant, uses AR to guide its technicians through complex aircraft maintenance procedures. By using AR-enabled tablets, technicians can access real-time instructions and 3D models, reducing errors and improving efficiency.
2. Quality Control and Inspection
AR is also being used to improve quality control and inspection processes in manufacturing. By overlaying digital models onto physical products, manufacturers can quickly identify defects and deviations from design specifications.
For instance, GE Appliances uses AR to inspect its refrigerators and washing machines during production. By using AR-enabled smart glasses, inspectors can quickly identify defects and take corrective action, reducing waste and improving product quality.
3. Predictive Maintenance
Predictive maintenance is another area where AR is making a significant impact. By analyzing real-time data from sensors and equipment, manufacturers can predict when maintenance is required, reducing downtime and improving overall efficiency.
Siemens, the German industrial conglomerate, uses AR to predict maintenance needs in its manufacturing facilities. By analyzing real-time data from sensors and equipment, Siemens can identify potential issues before they occur, reducing downtime and improving overall efficiency.
4. Virtual Assembly and Design
AR is also being used to improve the design and assembly of complex products. By using AR-enabled devices, designers and engineers can create virtual prototypes, reducing the need for physical prototypes and speeding up the design process.
For example, Ford Motor Company uses AR to design and assemble complex car parts, such as engine components and suspension systems. By using AR-enabled tablets, designers and engineers can collaborate in real-time, reducing errors and improving product quality.
5. Warehouse Management and Logistics
AR is also being used to improve warehouse management and logistics in manufacturing. By using AR-enabled devices, warehouse staff can quickly locate products, manage inventory, and optimize storage space.
DHL, the global logistics company, uses AR to optimize its warehouse operations. By using AR-enabled smart glasses, warehouse staff can quickly locate products, manage inventory, and optimize storage space, reducing costs and improving efficiency.
6. Supply Chain Optimization
AR is also being used to optimize supply chain operations in manufacturing. By analyzing real-time data from sensors and equipment, manufacturers can identify bottlenecks and inefficiencies in their supply chains, reducing costs and improving delivery times.
Procter & Gamble, the consumer goods giant, uses AR to optimize its supply chain operations. By analyzing real-time data from sensors and equipment, P&G can identify bottlenecks and inefficiencies, reducing costs and improving delivery times.
7. Enhanced Operator Performance
AR is also being used to enhance operator performance in manufacturing. By providing real-time instructions and guidance, AR-enabled devices can improve operator efficiency and reduce errors.
BMW, the German automaker, uses AR to enhance operator performance in its manufacturing facilities. By using AR-enabled smart glasses, operators can access real-time instructions and guidance, improving efficiency and reducing errors.
8. Digital Twinning
Finally, AR is being used to create digital twins of physical products and equipment. Digital twins are virtual replicas of physical products that can be used to simulate performance, test scenarios, and predict maintenance needs.
GE Digital, the software arm of General Electric, uses AR to create digital twins of its industrial equipment. By using AR-enabled devices, engineers can create virtual replicas of physical equipment, simulating performance and testing scenarios, reducing costs and improving efficiency.
Conclusion
Augmented reality is transforming the manufacturing sector in ways that were previously unimaginable. From remote guidance and training to predictive maintenance and digital twinning, AR is revolutionizing the way products are designed, produced, and maintained. As the technology continues to evolve, we can expect to see even more innovative uses of AR in manufacturing. Whether it's improving quality control, reducing downtime, or enhancing operator performance, AR is poised to play a critical role in the future of manufacturing.